From construction sites to manufacturing floors, oil rigs to laboratories, certain professions expose workers to hazards that can lead to serious injury or even death.
The key to preventing such tragedies lies in one of the most effective measures: the proper use of safety equipment. This blog delves into why safety equipment is vital in high-risk environments, the types of equipment needed, and how companies can foster a safety-first culture to protect their most valuable assets— their people.
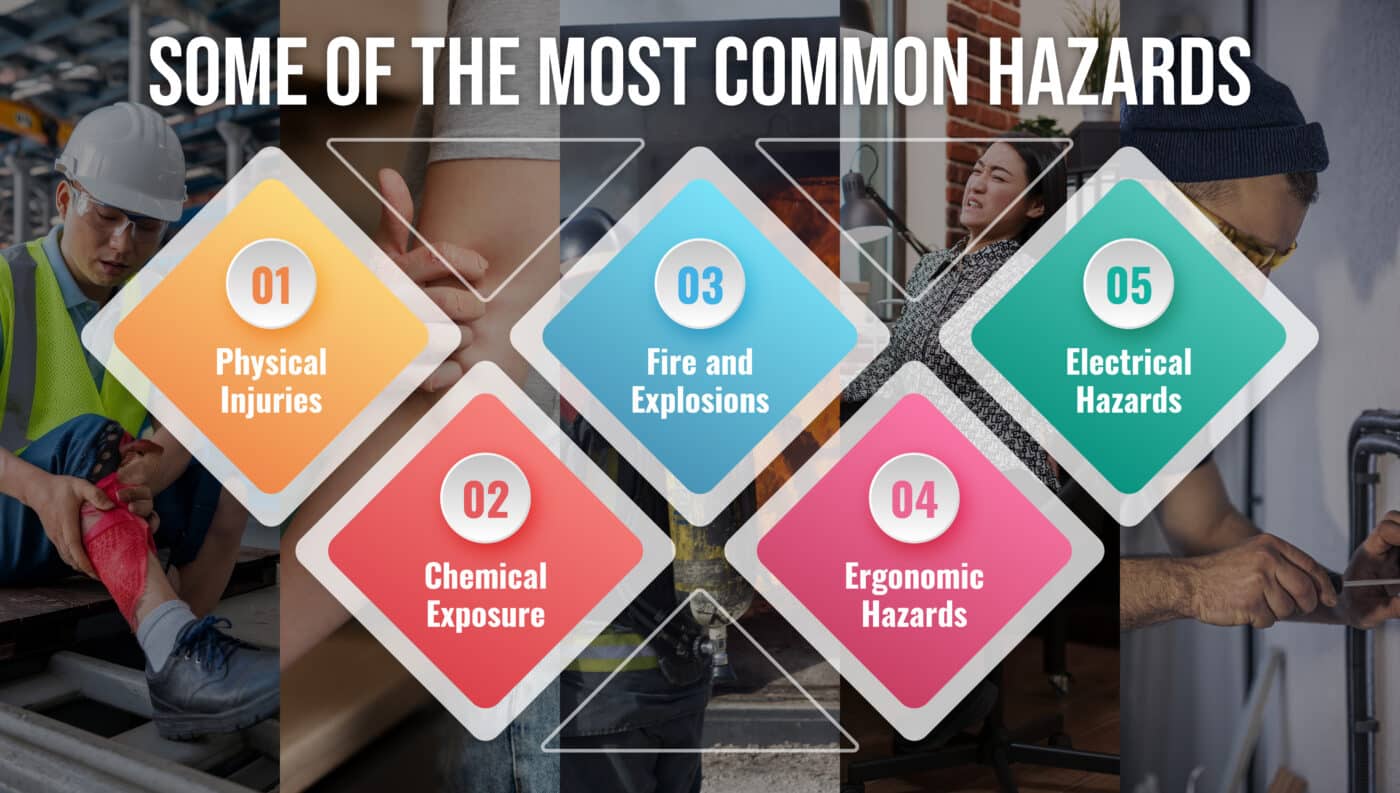
The Role of Safety Equipment in High-Risk Environments
Safety equipment serves as a crucial barrier between workers and the inherent dangers present in high-risk work environments. It provides immediate protection from physical harm, mitigates exposure to hazardous substances, and prevents accidents that could otherwise lead to severe consequences.
High-risk environments typically include construction sites, factories, warehouses, laboratories, energy plants, and any other workplace where dangerous machinery, chemicals, or unpredictable conditions are prevalent. Without adequate safety measures in place, the likelihood of accidents rises exponentially. Some of the most common hazards include:
- Physical injuries: Falling debris, machinery malfunctions, and slips and trips.
- Chemical exposure: Handling toxic substances, acids, or volatile chemicals.
- Fire and explosions: In environments dealing with flammable materials or high temperatures.
- Ergonomic hazards: Repetitive stress injuries or accidents due to improper lifting techniques.
- Electrical hazards: In jobs that involve heavy electrical systems or equipment.
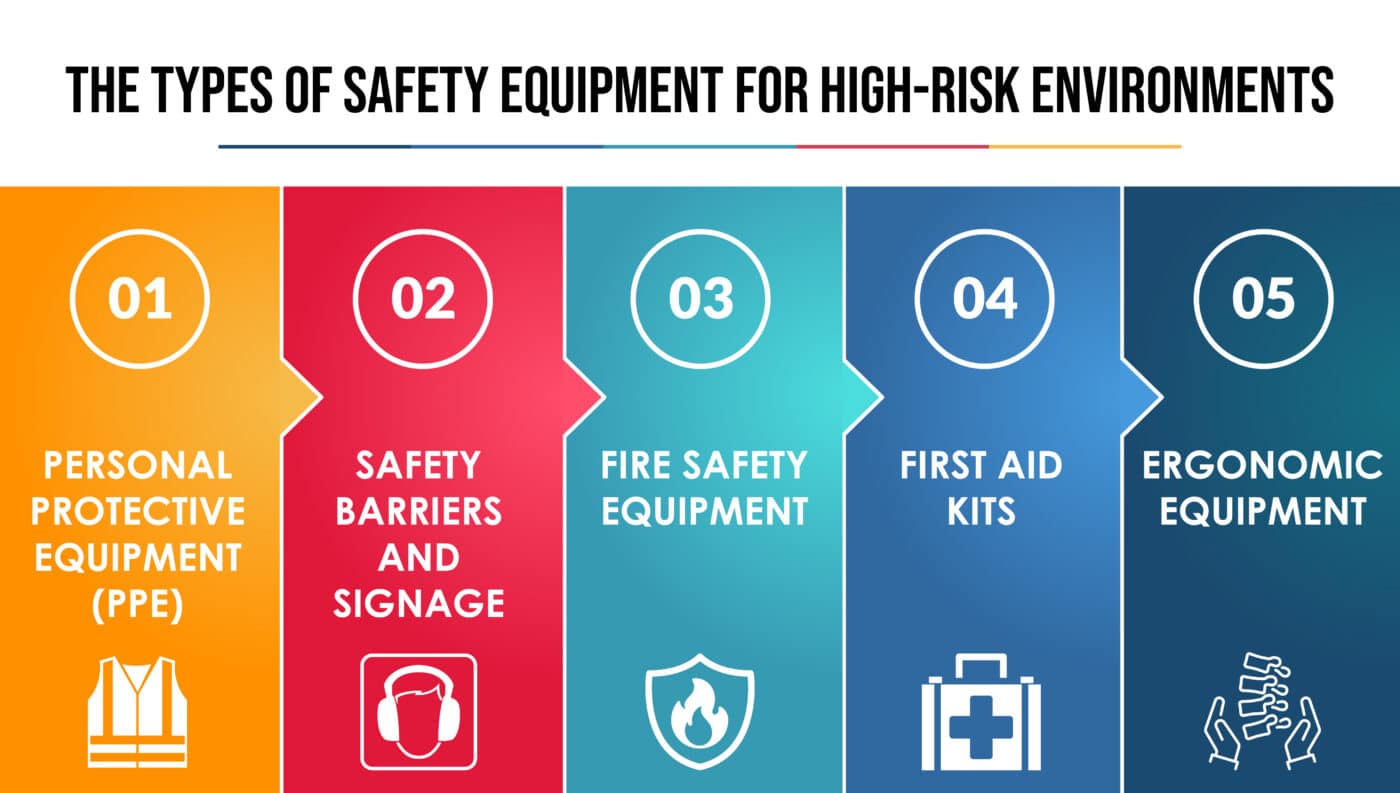
The Types of Safety Equipment for High-Risk Environments
The right safety equipment can vary depending on the nature of the work, but common categories include:
1. Personal Protective Equipment (PPE)
PPE is perhaps the most well-known and widely used category of safety equipment. It is designed to protect workers from physical, chemical, biological, and ergonomic hazards. Key types of PPE include:
- Helmets and Hard Hats: Essential for workers in construction or manufacturing, protecting the head from falling objects, debris, or collisions.
- Gloves: Various types of gloves (e.g., cut-resistant, chemical-resistant, heat-resistant) are necessary for handling dangerous materials and machinery.
- Safety Glasses or Goggles: Protect the eyes from flying debris, dust, chemicals, and bright lights, especially in environments like laboratories and construction sites.
- Ear Protection: In loud environments such as factories or construction sites, earplugs or earmuffs help prevent long-term hearing damage.
- Respirators and Face Shields: Used in workplaces with airborne hazards, such as toxic fumes, dust, or biological agents.
- Protective Clothing: Includes flame-resistant clothing, chemical-resistant suits, and high-visibility vests to keep workers safe from various environmental hazards.
2. Safety Barriers and Signage
Clear communication is vital in high-risk environments, and safety barriers or signs can prevent accidents by alerting workers to potential dangers. These could include:
- Safety Barriers and Guardrails: Protect workers from falling from heights or accessing dangerous machinery.
- Warning Signs and Labels: Indicate hazardous zones, like areas with electrical risks or chemicals, guiding employees to take extra precautions.
3. Fire Safety Equipment
In many high-risk environments, fire hazards are prevalent. Fire safety equipment is critical for preventing, containing, and extinguishing fires before they can cause widespread damage:
- Fire Extinguishers: Must be easily accessible and appropriate for the specific type of fire risk.
- Sprinkler Systems and Fire Suppression Systems: Designed to douse fires in case of emergency, especially in areas with high heat generation.
4. First Aid Kits
Accidents can happen even with the best preventive measures, which is why first aid kits are crucial. These kits should be stocked with essentials like bandages, antiseptic wipes, gauze, burn creams, and even more specialized equipment like defibrillators in certain industries.
5. Ergonomic Equipment
For industries like warehousing, manufacturing, and logistics, ergonomic tools are essential to reduce the risk of musculoskeletal injuries from lifting, bending, and repetitive motions. Adjustable workstations, ergonomic chairs, and lifting devices can all make a significant difference in worker comfort and safety.
How to Foster a Safety-First Culture
The presence of safety equipment alone is not enough to ensure worker protection. Equally important is fostering a culture of safety that prioritizes vigilance, training, and ongoing improvement. Here’s how companies can build and maintain a safety-first environment:
1. Comprehensive Training
Safety training should be an ongoing process, not a one-time event. All workers should undergo thorough training on the proper use of safety equipment, recognizing potential hazards, and responding to emergencies.
- Induction Training: New employees should be made aware of safety protocols and how to use safety equipment before they start work.
- Regular Refresher Courses: Periodic training ensures that employees stay up-to-date on safety procedures and understand new risks that may arise.
2. Regular Inspections and Maintenance
Safety equipment must be maintained in proper working order at all times. Regular inspections of equipment like helmets, goggles, and safety harnesses should be scheduled to ensure they’re functioning properly.
- Routine Audits: Conducting regular safety audits to check whether equipment is being used correctly and is up to code.
- Maintenance and Repairs: Equipment that is worn or damaged should be immediately repaired or replaced to prevent failure when needed most.
3. Clear Communication of Safety Protocols
Employers should ensure that safety standards are clearly communicated to all employees. This can include safety signage, digital communications, and regular meetings where safety concerns are discussed.
- Safety Briefings: Daily or weekly safety briefings can keep everyone on the same page about potential risks.
- Open Dialogue: Encouraging employees to report hazards or unsafe conditions is vital. Implementing an easy, anonymous way for workers to report safety issues can create a more proactive safety culture.
4. Incentivize Safety Compliance
Positive reinforcement can be an effective way to keep safety standards high. Consider offering rewards or recognition to teams or individuals who consistently follow safety protocols. This can help instill a sense of responsibility and pride in the workplace’s safety culture.
5. Emergency Preparedness Plans
No matter how much effort goes into preventing accidents, they can still happen. Having a well-documented and practiced emergency preparedness plan is essential. This includes:
- Evacuation Procedures: Ensuring all employees know the quickest and safest way to evacuate during a crisis.
- First-Aid Training: Having designated first responders and providing first-aid training to employees can help mitigate the effects of injuries before professional medical help arrives.
The ROI of Investing in Safety
While safety equipment and protocols may seem like a financial burden upfront, the long-term benefits are undeniable. Investing in the proper tools, training, and culture can lead to:
- Reduced Injury Rates: Fewer accidents mean fewer workers’ compensation claims, less downtime, and reduced medical costs.
- Higher Employee Morale: A safe work environment helps employees feel valued and supported, leading to increased productivity and retention.
- Compliance with Regulations: Ensuring that your company meets the safety standards required by regulatory bodies helps avoid costly fines and legal issues.
- Improved Reputation: Companies with strong safety records are more attractive to top talent and customers who prioritize ethical and responsible practices.
Conclusion
In high-risk environments, safety equipment isn’t just a legal obligation; it’s an essential investment in your team’s well-being. It helps protect workers from immediate threats, reduces the long-term impact of injuries, and fosters a culture of accountability and care.
By equipping your team with the right tools, investing in ongoing training, and embedding safety into your company’s DNA, you’re not just preventing accidents—you’re safeguarding your most valuable asset: your people. And that’s a win for everyone involved.